隨著新能源汽車市場(chǎng)的爆發(fā)式增長(zhǎng),電池托盤作為電池系統(tǒng)的核心承載結(jié)構(gòu),其制造成本與工藝效率成為車企供應(yīng)鏈優(yōu)化的關(guān)鍵環(huán)節(jié)。傳統(tǒng)焊接工藝存在熱變形大、良率低、能耗高等痛點(diǎn),而激光焊接自動(dòng)化技術(shù)憑借高精度、高效率、低能耗等優(yōu)勢(shì),正成為行業(yè)降本增效的核心解決方案。
一、激光焊接自動(dòng)化的核心技術(shù)優(yōu)勢(shì)
??1、高精度焊接與變形控制??
激光焊接通過聚焦高能光束實(shí)現(xiàn)微米級(jí)熱輸入,可將鋁合金電池托盤的平面度誤差控制在2毫米以內(nèi)。采用反變形技術(shù)與激光填絲焊工藝,焊接變形量較傳統(tǒng)攪拌摩擦焊降低50%以上,良率提升至99%。例如,某頭部企業(yè)通過激光填絲焊工藝,將6061鋁合金托盤的焊接速度提升至3m/min,同時(shí)將熱裂紋缺陷率降低至0.1%以下。
??2、高效率與高產(chǎn)能
全自動(dòng)產(chǎn)線集成攪拌摩擦焊、拉鉚等10余種工藝,單臺(tái)電池托盤全流程焊接僅需166秒,年產(chǎn)能達(dá)10萬(wàn)套。相較傳統(tǒng)CMT焊接,激光填絲焊速度提升3-5倍,且無(wú)需二次CNC加工。有案例顯示,激光焊接產(chǎn)線通過工藝優(yōu)化,將薄壁結(jié)構(gòu)(厚度≤3mm)的焊接效率提升40%,材料利用率達(dá)98%。
??3、材料與能耗優(yōu)化??
激光焊接可減少焊材浪費(fèi)(節(jié)約7%-12%),并通過精準(zhǔn)能量控制降低能耗。有數(shù)據(jù)顯示,自動(dòng)化產(chǎn)線能耗較人工焊接降低30%,配合視覺跟蹤系統(tǒng),焊后返工率從15%降至6%。
二、具體案例解析
1、項(xiàng)目背景
某頭部汽車零部件外資企業(yè)為滿足新能源汽車市場(chǎng)對(duì)電池托盤的高需求,打造了一條全自動(dòng)電池托盤產(chǎn)線。該產(chǎn)線需實(shí)現(xiàn)高精度、高效率的焊接工藝,同時(shí)滿足歐盟市場(chǎng)的嚴(yán)格質(zhì)量標(biāo)準(zhǔn)。
2、技術(shù)方案
該產(chǎn)線采用全自動(dòng)化激光焊接技術(shù),結(jié)合攪拌摩擦焊、拉鉚等多種工藝,打造了一條長(zhǎng)達(dá) 150 米、擁有 60 多個(gè)工位的智能產(chǎn)線。產(chǎn)線配備了高精度的視覺定位系統(tǒng)、焊縫跟蹤系統(tǒng)和機(jī)器人系統(tǒng),實(shí)現(xiàn)了從零件上料到焊接完成的全流程自動(dòng)化。
3、ROI 分析
-
設(shè)備投資與成本節(jié)約:激光焊接自動(dòng)化產(chǎn)線的初期投資較高,但通過提高生產(chǎn)效率和產(chǎn)品質(zhì)量,可顯著降低長(zhǎng)期成本。
-
生產(chǎn)效率提升:該產(chǎn)線的焊接速度極快,僅需 166 秒即可完成一臺(tái)電池托盤的全流程焊接,生產(chǎn)效率較傳統(tǒng)工藝提升了數(shù)倍。以年產(chǎn) 10 萬(wàn)套電池托盤計(jì)算,激光焊接自動(dòng)化產(chǎn)線可節(jié)省大量的人力和時(shí)間成本,顯著提高企業(yè)的經(jīng)濟(jì)效益。
-
投資回收期:根據(jù)行業(yè)數(shù)據(jù),激光焊接自動(dòng)化產(chǎn)線的投資回收期通常在 1-2 年左右。
4、效率提升數(shù)據(jù)
-
焊接速度:激光焊接速度可達(dá) 3m/min,是傳統(tǒng) CMT(冷金屬過渡焊接技術(shù))的 3-5 倍。
-
生產(chǎn)周期:激光焊接自動(dòng)化產(chǎn)線的全流程焊接時(shí)間僅為 166 秒,較傳統(tǒng)工藝大幅縮短。
-
良品率:激光焊接的良品率超 99%,較傳統(tǒng)焊接工藝的良品率(通常為 90%-95%)有顯著提升。如激光填絲焊智能裝備在鋁合金電池盒焊接中,變形量精度控制在 1 毫米以內(nèi),良品率超 99%。
三、成本控制策略的四大維度
??1、減少冗余工序??
激光焊接支持“一機(jī)多用”,例如集成攪拌摩擦焊與機(jī)加工的復(fù)合設(shè)備,單臺(tái)完成焊接與表面處理,節(jié)省30%設(shè)備投資。企業(yè)可以通過激光-電弧復(fù)合焊技術(shù),將電池托盤結(jié)構(gòu)件的加工工序從5道減至2道。
??2、自動(dòng)化產(chǎn)線
全自動(dòng)化產(chǎn)線減少80%人工干預(yù),有一家頭部車企部署6軸機(jī)械臂焊接單元,人力成本降低65%,實(shí)現(xiàn)24小時(shí)連續(xù)生產(chǎn)。數(shù)據(jù)顯示,自動(dòng)化焊接使單件人工成本從120元降至35元。
??3、質(zhì)量管控
激光焊接缺陷率低于0.1%,較傳統(tǒng)工藝(2%-3%)顯著優(yōu)化。以年產(chǎn)10萬(wàn)套托盤計(jì)算,年減少?gòu)U品損失超500萬(wàn)元。通過在線監(jiān)測(cè)系統(tǒng),可將焊縫氣孔率控制在0.05%以內(nèi)。
??4、供應(yīng)鏈協(xié)同
通過整合上下游供應(yīng)商,實(shí)現(xiàn)鋁材采購(gòu)成本降低8%,物流效率提升20%。有企業(yè)通過采用區(qū)域化供應(yīng)鏈布局,將原材料交付周期從15天縮短至7天。
激光焊接自動(dòng)化技術(shù)通過工藝革新與全鏈路協(xié)同,為新能源汽車電池托盤制造提供了可量化的成本控制方案。行業(yè)實(shí)踐表明,其ROI可達(dá)200%以上,同時(shí)推動(dòng)制造體系向高效、智能、綠色方向轉(zhuǎn)型。
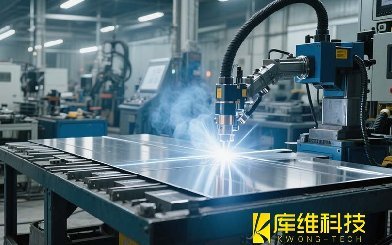
激光焊接技術(shù):鋁合金激光焊與激光-電弧復(fù)合焊
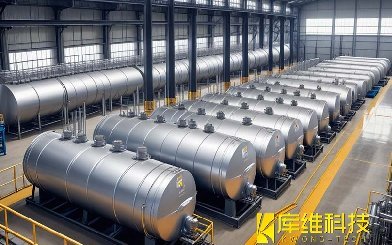
大型罐體焊切自動(dòng)化產(chǎn)線的多領(lǐng)域應(yīng)用
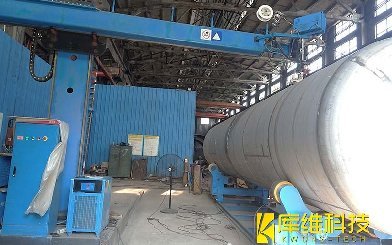
大型罐體焊切自動(dòng)化產(chǎn)線實(shí)例與搭建
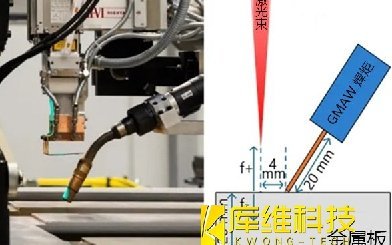
激光-電弧復(fù)合焊接技術(shù)如何成功焊接20mm厚的鋼板
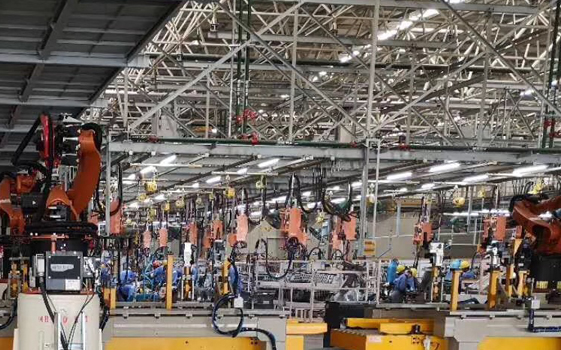
工業(yè)自動(dòng)化產(chǎn)線有幾大機(jī)器人?你都知道嗎?